Comprehensive Guide to Industrial Electronic Equipment
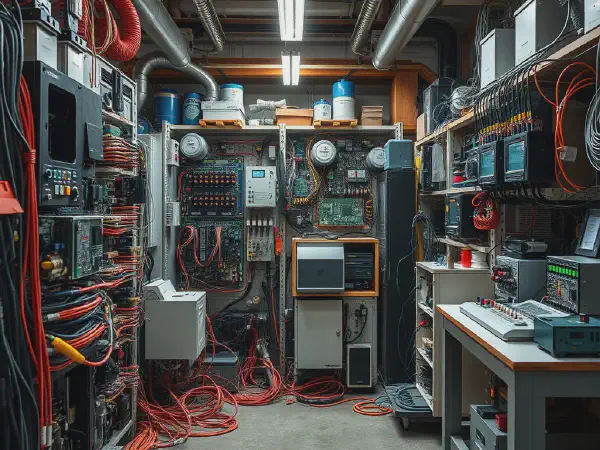
Understanding Industrial Electronic Equipment
Industrial Electronic Equipment plays a pivotal role in the modern manufacturing and process control industries. It encompasses a wide range of devices and systems that are used to monitor, control, and optimize industrial processes. The significance of industrial electronic equipment can be traced back to its capacity to enhance efficiency, reduce manual labor, and improve precision in various operations. With the continual advancement in technology, the scope of industrial electronic equipment has expanded, making it an indispensable component in today's industry.
The evolution of Industrial Electronic Equipment has led to the integration of sophisticated technologies such as automation, sensors, and control systems. This strategic incorporation of electronic frameworks allows manufacturers to achieve higher productivity levels while maintaining stringent quality standards. Additionally, industrial electronic equipment includes devices such as programmable logic controllers (PLCs), industrial computers, and various types of sensors, all of which are pivotal in facilitating seamless operations within factories and production lines.
Furthermore, industrial electronic equipment contributes significantly to safety and risk management within industrial environments. The implementation of advanced control systems and safety protocols not only protects workers from potential hazards but also ensures that machinery operates within safe parameters. By continuously monitoring equipment performance and providing real-time feedback, these electronic systems help to prevent operational failures and accidents, which is crucial for overall workplace safety.
In summary, Industrial Electronic Equipment encompasses a vast array of tools and devices designed to enhance operational efficiency, safety, and productivity in various industrial settings. As industries continue to adapt to new technological advancements, the role of industrial electronic equipment will likely become even more central in creating efficient and safe working environments.
In conclusion, Industrial Electronic Equipment is the backbone of industrial operations. As the technology progresses, catering to new demands and challenges, investing in high-quality electronic equipment will be imperative for businesses to remain competitive in an ever-evolving market.
The reliability and performance of an industrial pc make it essential for modern manufacturing processes.
Types of Industrial Electronic Equipment
Control systems are at the heart of industrial electronic equipment, facilitating automated processes across manufacturing and other industrial sectors. These systems, including Programmable Logic Controllers (PLCs), Supervisory Control and Data Acquisition (SCADA), and Distributed Control Systems (DCS), regulate machinery and streamline operations by executing programmed instructions based on real-time data inputs.
To enhance operational efficiency, businesses increasingly rely on esis software for their automation needs.
Sensors and actuators are crucial components in process control applications, enabling accurate measurement and response to varying conditions. Sensors collect data on parameters such as temperature, pressure, and flow, while actuators convert electrical signals into physical movements to control machinery and equipment. Their complementary functions ensure precision in industrial processes, leading to enhanced productivity and safety.
Industrial computers have transformed the way industries operate, offering robust computing solutions designed specifically for challenging environments. These systems are used for data analysis, process visualization, and machine control. Their resilience against vibrations, dust, and temperature variations makes them suitable for deployment in factories, leading to greater efficiency and improved decision-making processes.
Utilizing a pdf temperature data logger ensures accurate monitoring of crucial temperature parameters in industry.
Power supplies are integral to the operation of industrial electronic equipment, providing consistent and reliable energy to various components. The importance of power supplies lies in their role in maintaining system stability and performance. This includes uninterruptible power supplies (UPS) capable of sustaining operations during power outages, ensuring continuity and reducing downtime.
Applications of Industrial Electronic Equipment
The role of industrial electronic equipment in manufacturing processes cannot be overstated. From automation of assembly lines to real-time quality control systems, these tools facilitate the seamless production of goods while optimizing resource utilization. The efficiency brought by such equipment significantly reduces operational costs and enhances productivity.
In energy management systems, industrial electronic equipment enhances monitoring and control of energy consumption, enabling businesses to reduce costs and improve sustainability. Smart meters, control sensors, and data analytics tools allow for efficient energy distribution and consumption tracking, leading to informed decisions on energy usage.
The integration of industrial electronic equipment in transportation and logistics enhances operational efficiency by streamlining processes such as inventory management, shipment tracking, and automated warehousing. Real-time data collection and communication improve logistics coordination, ultimately leading to faster delivery times and reduced operational costs.
Security systems integrated with industrial electronic equipment play a crucial role in safeguarding assets and personnel. Surveillance cameras, access control systems, and alarm systems powered by electronic technologies provide real-time monitoring and alert responses, ensuring a secure working environment and compliance with safety regulations.
Maintenance of Industrial Electronic Equipment
Routine maintenance practices for industrial electronic equipment are essential for ensuring longevity and optimal performance. Regular inspections, cleaning, and testing help identify potential issues before they escalate into significant breakdowns, thereby minimizing downtime and maintenance costs.
Troubleshooting common issues in equipment involves understanding the various components and their functions. Quick response to malfunctioning parts, assisted by diagnostic tools and software, helps restore functionality efficiently. Knowledge of standard fault conditions aids in faster resolution of problems, ensuring minimal disruption to operations.
Software updates are crucial in maintaining industrial electronic systems to enhance their functionality and security. Regular updates not only patch vulnerabilities but also improve performance and compatibility with newer technologies, keeping the systems efficient and secure against potential threats.
Safety protocols for handling electronic equipment involve comprehensive training and adherence to operational guidelines to prevent accidents. Personal protective equipment (PPE), proper training, and established safety procedures are necessary to ensure that personnel can work safely around electronic systems, minimizing the risk of injury.
Future Trends in Industrial Electronics
The impact of the Internet of Things (IoT) on industrial electronic systems is profound, enabling connectivity and data exchange among various devices. IoT technologies facilitate real-time monitoring, predictive maintenance, and optimization of industrial processes, paving the way towards fully integrated smart factories.
Advancements in automation technology continue to transform industries, with the integration of robotics, AI, and machine learning into production processes. These advancements enhance efficiency, precision, and flexibility, making it possible to adapt quickly to changing market demands and improve overall productivity.
Sustainable practices in electronic equipment usage are becoming increasingly important as industries seek to minimize their environmental footprints. Energy-efficient components, recycling programs, and eco-friendly manufacturing processes are gaining prominence, aligning with global sustainability goals.
The integration of AI in industrial processes is set to revolutionize operations further by enabling advanced analytics, real-time decision-making, and process optimization. AI can learn from historical data, providing insights that drive efficiency and innovation in manufacturing and other industries.
Safety Standards for Industrial Electronic Equipment
OSHA regulations related to electronic equipment help ensure a safe workplace by establishing standards that protect workers from electrical hazards. These guidelines encourage the use of proper safety equipment and the implementation of effective safety measures concerning industrial electronic installations.
Following ISO standards is essential for organizations to guarantee quality and safety in their industrial operations. These standards dictate the requirements for effective quality management systems and risk management practices, supporting continuous improvement and operational excellence in industries worldwide.
Common safety practices in industrial environments include regular training sessions, safety audits, and implementation of emergency response plans. Promoting a culture of safety and accountability contributes to minimizing risks associated with the use of electronic equipment in industrial settings.
Evaluating risk and implementing safety measures involves conducting thorough assessments of potential hazards related to industrial electronic equipment. This proactive approach ensures that safety protocols are in place, reducing the likelihood of accidents and enhancing overall safety in the workplace.